¿Qué es un FMECA?
El FMECA (Failure Mode, Effects, and Criticality Analysis - AMFEC en castellano: Análisis de Modos de Fallos, Efectos y su Criticidad ), es una metodología para identificar y analizar todos los modos de fallos potenciales de las diferentes partes de un sistema, los efectos que estos fallos puedan tener en el sistema, cómo evitar los fallos y/o mitigar sus efectos en el sistema.
Dicho de otro modo y simplificando, el FMECA es una técnica para identificar, priorizar y eliminar posibles fallas del sistema (a nivel de diseño o proceso). Los FMECA básicamente se diferencian de FMECA de Diseño y FMECA de Proceso: el primero hace referencia al producto o sistema en sí, el segundo se centra en los problemas derivados de cómo el equipo es fabricado, mantenido u operado.
Inicialmente el FMECA se llamaba FMEA o AMFE. La C es un nuevo parámetro que cada vez se utiliza más, el cual indica la criticidad o gravedad de los diversos efectos de los fallos, pudiendo priorizar su importancia.
¿Para que se utiliza un FMECA?
- Tener un criterio objetivo de selección de alternativas de diseños durante las fases iniciales de un desarrollo de un producto o sistema
- Tener un método para considerar todos los modos de fallo posibles así como sus efectos
- Listar posibles fallos e identificar la gravedad de sus efectos
- Desarrollar criterios para ejecutar un plan de pruebas robusto y eficaz para la detección de problemáticas
- Acumular conocimiento para futuros desarrollos y cambios de diseño
- Proporcionar una base para la planificación del mantenimiento
- Proporcionar una base para el análisis de fiabilidad RAMS
¿Como se lleva a cabo un FMECA? A continuación describimos los 4 pasos esenciales de un proceso FMECA
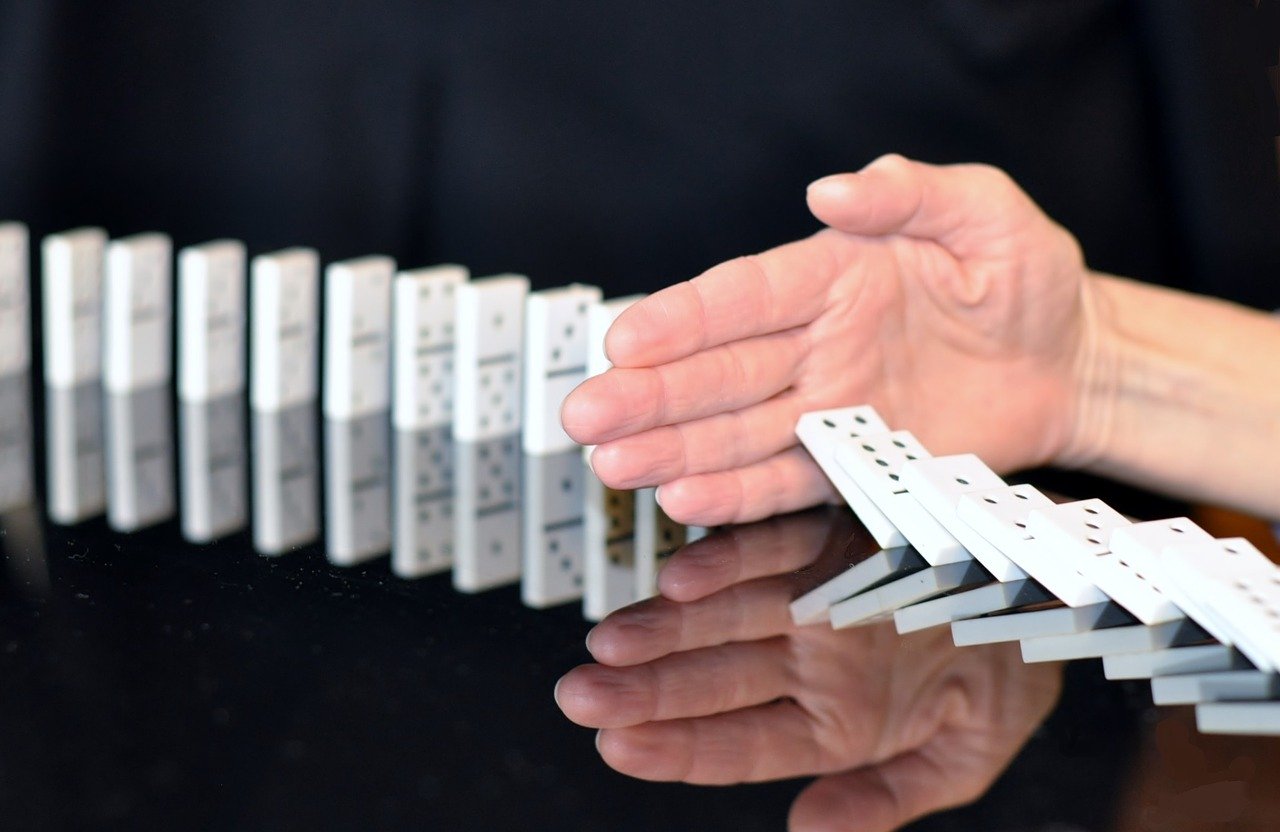
Paso 1: Preparación del FMECA
Inicialmente debe definirse correctamente el sistema a analizar teniendo claro cuales son los límites del sistema, es decir, que partes deben incluirse y cuáles quedan excluidas del análisis FMECA, teniendo en cuenta que los interfaces del límite del equipo a analizar también deben incluirse en el análisis. También es importante tener claras las condiciones operativas y ambientales a considerar. La temperatura o el estrés mecánico, por ejemplo, juegan un papel fundamental en los modos de fallo de los equipos.
Por otro lado es importante tener toda la información necesaria del sistema a analizar, incluidos los esquemas, diagramas de bloques, lista de componentes, información de interfaces, descripciones funcionales, etc. Un FMECA se lleva a cabo entendiendo lo que hace el sistema porque deberá verse como los fallos afectan al correcto funcionamiento del sistema. Por tanto, entender que significa correcto funcionamiento es necesario. Por último, si se dispone recomendamos siempre utilizar el retorno de la experiencia (REX) en procesos parecidos y/o productos parecidos del pasado. También puede recomendamos consultar a los proveedores de los componentes que vayamos a analizar nuestra intención de llevar a cabo un FMECA con la intención que nos hagan llegar toda la información de sus componentes al respecto.
Paso 2: Análisis de la estructura del sistema
Llevar a cabo un FMECA puede
llegar a verse como algo imposible de gestionar por su complejidad y
laboriosidad. De este modo, debe dividirse el sistema en unidades o componentes
manejables, generalmente de forma que tengan sentido desde el punto de vista de
la arquitectura de sistema desarrollada para la elaboración del producto. A
partir de aquí, hacer pequeños FMECAs de cada bloque obteniendo modos de fallos
totalizados de cada bloque para ver como estos afectan unos componentes
respecto a otros. Evidentemente, siempre que sea posible debe simplificarse el
análisis lo cual, en la mayoría de veces implica, analizar cuanto "más arriba
mejor", los modos de fallo de los componentes. Acostumbra a dificultar cuanto
más bajemos al análisis atómico (al mínimo componente) el sistema, aunque a
veces (sobretodo las primeras veces cuando no se reutiliza componentes), es
totalmente necesario. Como se identifica enseguida, utilizar bloques de una
arquitectura reutilizados y donde el FMECA ya esté hecho, representará una
ventaja en tiempo y coste importantísimo.
Paso 3: Análisis de fallos y preparación de las tablas FMECA
Para los primeros FMECAS que se llevan a cabo, la empresa debe decidir que plantilla utilizar. La plantilla normalmente se resume en unas columnas en una hoja de cálculo o utilizando alguna herramienta específica para el desarrollo de FMECA. Leedeo recomienda a sus clientes la siguiente plantilla como base para crear su propia a medida que evoluciona y coge experiencia en este tipo de actividades.
Para cada elemento del sistema el análisis debe considerar todas las funcionalidades de los elementos en todos sus modos operativos, y analizar si cualquier fallo del elemento puede resultar en un efecto inaceptable del sistema.

En sistemas RAMS donde la seguridad es un factor de diseño, acostumbramos a recomendar de ampliar en el "Efecto Producido en el Sistema", una nueva fila con las siguientes columnas para hacer check: efecto sobre la seguridad, efecto sobre la fiabilidad.
Paso 4: Revisión del FMECA ejecutado y acciones correctivas
Una vez se ha llevado a cabo todo el análisis FMECA, se acostumbra a llevar una puesta en común, donde se recomienda que todos los componentes del equipo del proyecto participen: el jefe de proyecto, el ingeniero de diseño y el ingeniero de procesos, el ingeniero RAMS, el ingeniero responsable del mantenimiento, etc.
El objetivo del equipo de trabajo es estudiar las hojas de trabajo del FMECA para decidir si el sistema es aceptable tal como se encuentra, identificar mejoras factibles del sistema y las que se implementarán finalmente con un orden de prioridad. Sin ser estrictos, recomendamos utilizar normalmente este "check-list" para buscar soluciones a los problemas detectados: cambios de diseño, cambios en los procedimientos o en la manera de como debe utilizarse el equipo, cambio de componentes como modos de fallo diferentes, uso de sistemas o dispositivos de advertencia de un suceso que genera un fallo, mitigar los efectos con alguna incorporación al diseño.
Conclusión
Un FMECA, FMEA, AMFE o AMFEC soc actividades típicas y necesarias de un proceso de análisis RAMS. Para tener un sistema o producto bajo control desde el punto de riesgos, es imprescindible conocer de que manera falla, pudiendo predecir y mitigar de antemano sucesos no deseados. En Leedeo Engineering tenemos una dilatada experiencia en el desarrollo de estas actividades RAMS. No dude en contactar con nosotros >>.
En Leedeo Engineering, somos especialistas en el desarrollo de proyectos de RAMS Ferroviaria, dando soporte a cualquier nivel requerido a las tareas RAM y de Safety, y tanto a nivel de infraestructura o equipamiento embarcado.
¿Te interesan nuestros artículos sobre Ingeniería RAMS y Tecnología?
Inscríbete en nuestra newsletter y te mantendremos informado de la publicación de nuevos artículos.