Mantenimiento Centrado en la Fiabilidad: el RCM. (Reliability Centered Maintenance)
En este artículo vamos hacer una introducción al RCM (Reliability Centered Maintenance). Es decir, el mantenimiento centrado o basado en la fiabilidad de la instalación y de todos sus componentes. El uso de la fiabilidad como el conductor principal de esta estrategia de mantenimiento cada vez más utilizada por sus beneficios, permite utilizar metodologías de la Ingeniería RAMS que pasan a ser decisivas para, sobre todo, el análisis y el diseño del plan de mantenimiento.
Introducción
Como es sabido, el desarrollo de una estrategia adecuada de mantenimiento pasa por definir un conjunto de procesos y recursos en forma de unos planes de mantenimiento, que dan respuesta y/o están soportadas por 4 conceptos básicos:
El primero de ellos es la teoria y modelos del mantenimiento y de la mantenibilidad. En efecto, el estado del arte y los conocimientos sobre todo sectoriales en el ámbito del mantenimiento, permite partir de una base de conocimiento estándar en los sectores o industrias que se aplica de forma transversal en todos los players del mismo.
El segundo es la propia experiencia de la empresa u organización. No hay ninguna duda que de forma agregada a los conocimientos del sector, existe un conocimiento, basado en su mayor parte en la experiencia, de cada uno de los actores que llevan a cabo procesos de mantenimiento.
En tercer lugar, se identifica un conocimiento transversal en todas las industrias que provienen de los fabricantes o integradores de los equipos, productos o sistemas, entendiendo como fabricantes aquellas empresas que diseñan y manufacturan equipos que acabarán instalados y en servicio dentro del ámbito de un sistema el cual debe mantenerse.
Y finalmente y de nuevo muy asociado a las diferentes industrias pero también a las regiones geográficas o económicas, el conjunto de legislaciones, directivas o estándares que deben cumplirse en materia del mantenimiento y de la mantenibilidad. En referencia a este último punto, Leedeo Engineering (www.leedeo.es) por ejemplo, aporta el bagaje y la experiencia del uso de las normativas CENELEC ferroviarias que especifican los requisitos en cuanto a la mantenibilidad de los sistemas ferroviarios en la Unión Europea (CENELEC EN 50126). Aunque la normativa CENELEC ferroviaria es de origen Europeo, esta se está utilizando de forma masiva en los 5 continentes.
¿Qué es el Mantenimiento Centrado en la Fiabilidad o RCM?
El mantenimiento centrado en la fiabilidad es una aproximación sistemática del mantenimiento, analizando y teniendo en cuenta la forma en que los sistemas pueden fallar, priorizando la seguridad y la economía (desde el punto de vista de la rentabilidad del activo bajo mantenimiento), que permiten identificar y clasificar las tareas de mantenimiento preventivo eficaces y aplicables. Por tanto, con un objetivo muy claro y directo el Mantenimiento Centrado en la Fiabilidad trata de: reducir los costes de mantenimiento, enfocándose en las funciones más importantes del sistema y evitando o eliminando las acciones de mantenimiento que no son estrictamente necesarias.
A continuación presentamos los 5 pasos que en Leedeo Engineering utilizamos para implantar un mantenimiento centrado en la fiabilidad en un activo o conjunto de activos, ya sea en una línea férrea, una línea de producción de bienes, un tren o un avión o cualquier mega infraestructura.
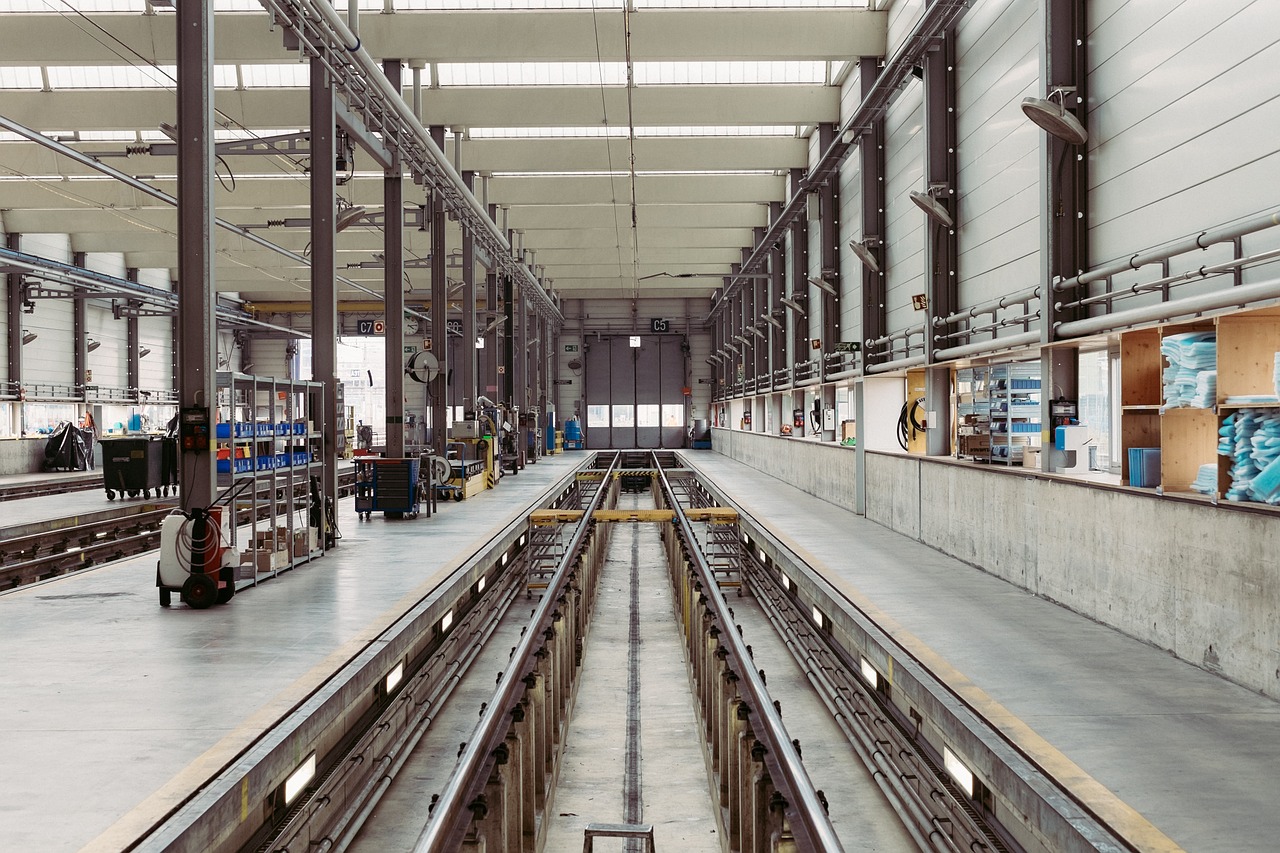
Preparación
El primer paso es diseñar un grupo de trabajo que implementará el nuevo sistema de mantenimiento centrado en la fiabilidad. Como es natural en estos casos, la involucración de personal con experiencia y conocimientos en la materia marcará la diferencia entre el éxito y el fracaso.
El segundo paso del proceso de Preparación es definir y aclarar los objetivos y alcance de trabajo. En este sentido, es de relevancia destacar la importancia de la definición del scope o alcance del procedimiento de mantenimiento. Es muy habitual que en los interfaces entre uno y otro activo o sistemas, se dejen partes fuera del alcance de todos los grupos de trabajo o iniciativas, asumiendo que es labor de otro equipo o plan de mantenimiento el llevar a cabo la gestión de aquel activo. Por tanto, la buena definición de los boundaries (los límites de actuación) y que se comuniquen a todas las partes interesadas, será muy importante. Este concepto nos lleva a la definición propia de las limitaciones del análisis y, por tanto, contestar a la pregunta, ¿hasta dónde llegaremos y hasta dónde dejaremos de llegar?
En este mismo punto, también definiremos los objetivos. En este sentido, se acostumbran normalmente a definir el objetivo de disponibilidad, por ejemplo, anual de la instalación o en cada punto crítico de la instalación con impacto sobre el desarrollo del negocio.
El tercer y último paso es recopilar y normalmente (debido a su deficiencia) generar documentación, esquemas y diagramas de proceso para poder tener un buen punto de partida de trabajo. Tocará en las siguientes fases analizar el detalle de la instalación y de lo que sucede en ella y, por tanto, tenerlo documentado es imprescindible. Este paso puede considerarse como una auditoría documental ya que, en la mayoría de ocasiones, deberemos buscar, encontrar y ponerle remedio tanto a la falta de documentación como a discrepancias entre la documentación generada y la instalación real.
Desarrollo de un análisis de fallas funcionales (functional failure analysis)
Concluida la etapa de preparación, la primera etapa de análisis asociada a técnicas RAMS para la implantación de un RCM pasa por el desarrollo de un análisis de fallos funcionales o FFA. El objetivo de un FFA es triple. El primero es identificar y describir las funciones requeridas para cada uno de los equipos o elementos de la instalación o sistema, describiendo las interfaces de entrada y salida para que este puede operar de forma correcta. Identificado el equipo y sus interfaces, el segundo paso es identificar la forma en que el sistema puede fallar en sus diferentes modos de funcionamiento. Para cada fallo funcional que puede tener el equipo, debe analizarse su criticidad con dos factores: "impacto en" y "severidad", en los siguientes términos:
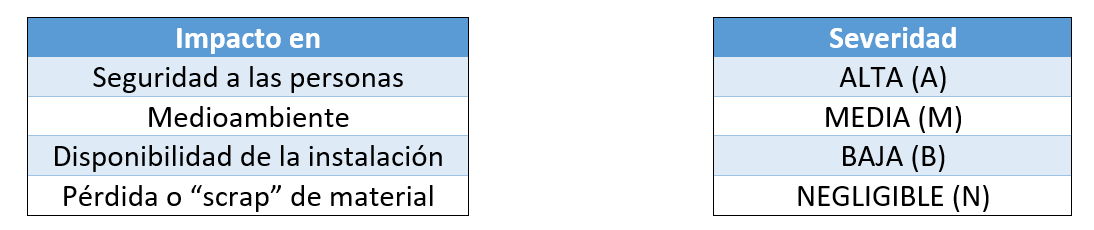
Finalmente será importante identificar y definir la ocurrencia de la aparición de dicho fallo: la frecuencia de ocurrencia, ya sea mediante una aproximación cualitativa o, si la información está disponible, de forma cuantitativa. Para una aproximación cualitativa se puede utilizar esta tabla de probabilidades de ocurrencia:
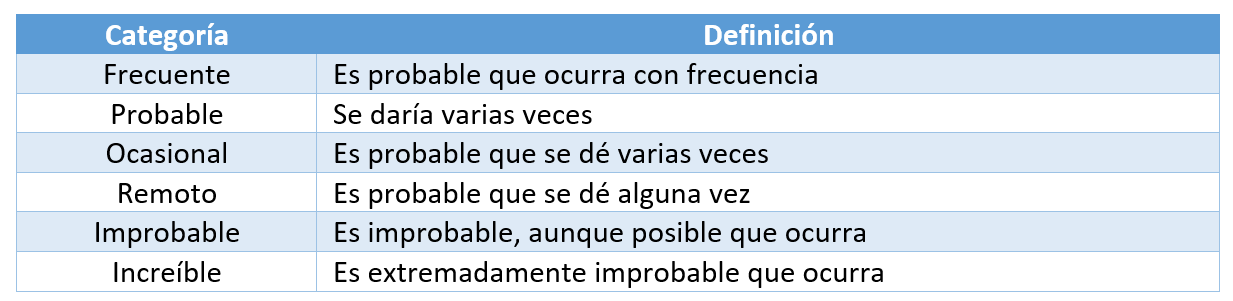
Por tanto, para cada uno de los subsistemas de nuestra arquitectura de instalación documentado en el paso de preparación, tendremos una tabla con esta información del FFA, pudiendo tener una visión clara de que hacen, como se interfazan con el resto del sistema, como fallan y que importancia o impacto tiene el fallo de cada uno de ellos.
Clasificación de sub-sistemas
La segunda etapa de análisis RAMS pasa por clasificar cada uno de los sub-sistemas identificados y analizados en el FFA en las 3 categorías siguientes. A nivel práctico esto implica añadir 3 columnas en la tabla inicial desarrollada, marcando por ejemplo con una "X" en que categoría se encuentra cada fallo:
- Categoría 1: Marcamos los subsistemas con fallos del FFA que tienen consecuencias ALTA o MEDIA para cualquiera de los destinos de impacto.
- Categoría 2: Marcamos los subsistemas con fallos del FFA que tienen probabilidad de ocurrencia frecuente o probable y se caracterizan por tener costes de reparación altos, baja mantenibilidad, plazos de entrega de repuestos elevado, obsolescencia de componentes o que su mantenimiento correctivo requiere personal externo fuera de nuestro control.
- Categoría 3: Marcamos el resto de subsistemas como fallos del FFA que están fuera de la Categoría 1 o 2.
Como puede imaginarse, el objetivo de clasificación es la priorización. En efecto, centraremos nuestros planes de acción y mejora en los sub-sistemas de Categoría 1 y 2. Y dejaremos para un segundo loop de mejora de nuestro sistema organizativo de mantenimiento, los sub-sistemas de Categoría 3.
Desarrollo de un FMECA (Failure Mode and Effects Critical Analysis) o Análisis de modos de fallos y sus efectos, teniendo en cuenta su criticidad (AMFEC)
Una vez clasificados los sub-sistemas para su criticidad en el paso anterior, el tercer paso del análisis RAMS de una implantación RCM es, de nuevo, evolucionar la tabla FFA hacia un FMECA completo añadiendo nuevos detalles hacia el mantenimiento, es decir, enriqueciendo la tabla desarrollada en la FFA con los siguientes parámetros (en las columnas) para cada uno de los fallos encontrados y para cada uno de los sub-sistemas:
- Efecto que produce el fallo.
- Mecanismo del fallo. Es decir, como se produce el fallo. Debido a que o cual es su origen.
- Acción de mantenimiento que se deberá hacer.
- Capacidad que se tiene para detectar el fallo producido.
- Intervalo para medir si el fallo ha aparecido.
La finalidad de esta fase tiene dos objetivos. El primero es concluir que la criticidad de un fallo con el efecto que produce y la capacidad que tenemos de que sea detectado obliga a implantar cambios en los propios activos que:
- bien reduzcan la criticidad o que minimicen el efecto que producen o finalmente,
- la detección de fallo sea adecuada a los dos parámetros anteriores,
- tengamos que mejorar su detección y alarma producida frente la aparición de dicho fallo.
El segundo objetivo es el establecimiento de las acciones de mantenimiento preventivo que tenemos que llevar a cabo para que dichos fallos no generen el efecto indeseado que hemos identificado.
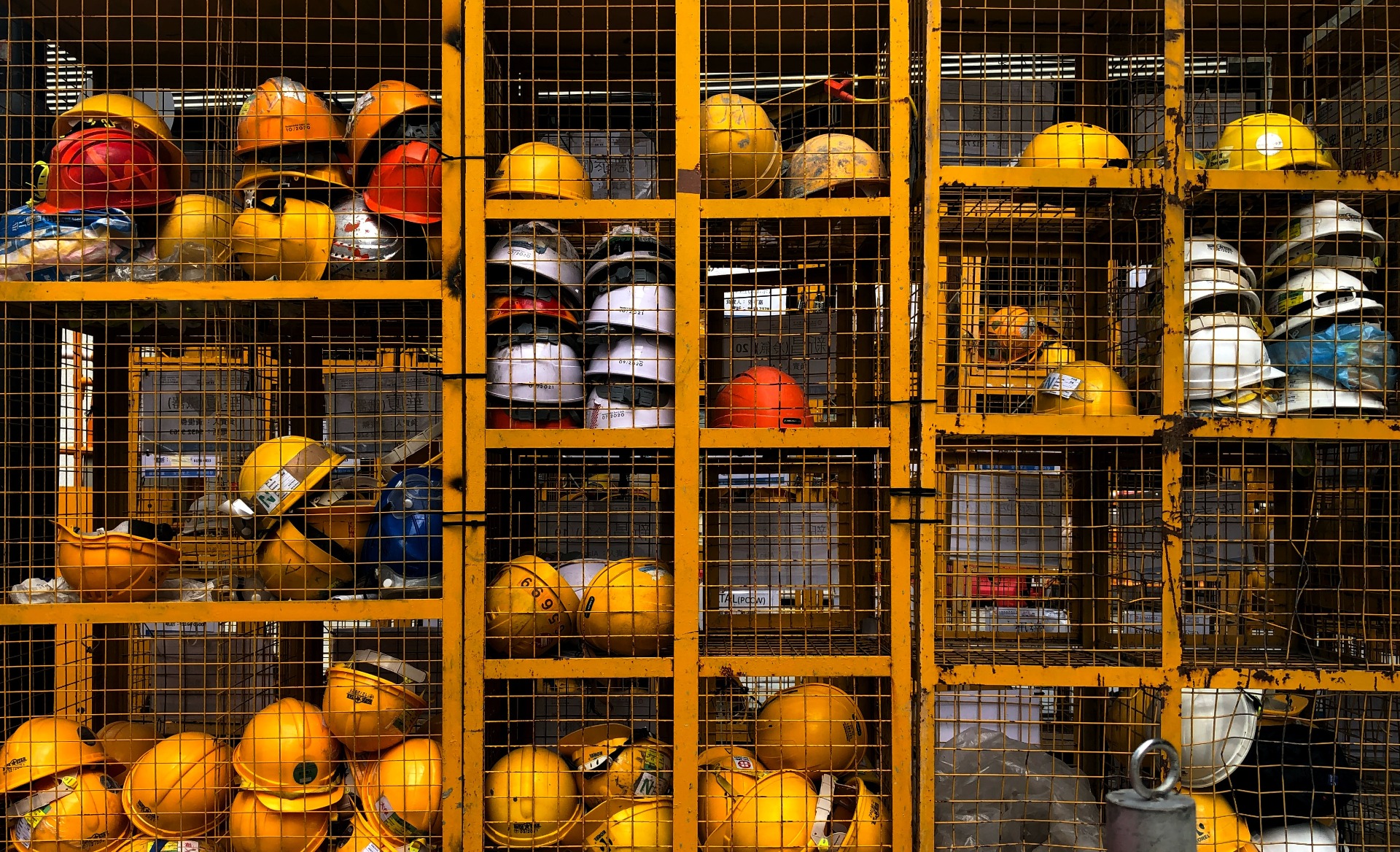
Diseño de las acciones de mantenimiento
El último paso es la definición de nuestras acciones de mantenimiento en base a cinco tipos de acciones diferentes:
- revisiones programadas,
- reemplazos de componentes (LRUs) programados,
- prueba de funcionalidad programada,
- tarea programada frente a la aparición de una condición (muchas veces esta tarea puede ser generada por un proceso de mantenimiento predictivo),
- y acción correctiva.
Como vemos, la mayoría de las actividades que llevaremos a cabo (las cuatro de las cinco acciones) son de tipo preventivo. El objetivo final del RCM es que las acciones correctivas tiendan a 0 y que todas las acciones de mantenimiento puedan ser preventivas. Las actividades preventivas son predecibles, controladas, sin efecto "caos" que produce la necesidad de poner en servicio de nuevo un equipo frente a un acción correctiva y, sobretodo, tienden a ser mucho más económicas que una acción correctiva.
Los mantenimientos preventivos, al fin y al cabo, deben ser vistos como aquellas actividades que nos permitirán evitar un fallo, detectar el inicio de un fallo, o descubrir un fallo oculto.
El proceso para determinar cada una de las actividades de mantenimiento preventivo siguen una lógica muy sencilla pero que es importante aplicar de forma estricta para asegurar un mantenimiento correctivo que ayuda a aplacar aquellas situaciones no deseadas:
- ¿Tenemos las posibilidad de tener un indicador o alarma de la aparición de este fallo?
- Si la respuesta es que sí se debe programar una tarea a la aparición de esta condición.
- Si la respuesta en que no, debemos preguntarnos si este fallo impacta en la tasa de fallo general de nuestro sistema o instalación. Si efectivamente impacta programaremos dos actividades posibles: su revisión (si es posible) o programaremos su substitución.
- Si el fallo no impacta inicialmente en la tasa de fallo general de nuestro sistema (imaginemos porque tenemos soluciones redundadas, por ejemplo), programaremos actividades de prueba de funcionalidad.
Finalmente, en cuanto a las acciones de mantenimiento correctivo, estas deben verse como decisiones deliberadas ya que se llega a la consclusión que las tareas de mantenimiento preventivo no son posibles o su coste es menos favorable. De todos modos, es importante recalcar que el mantenimiento correctivo, en general, suele ser la opción más costosa, y sólo debe usarse en componentes de bajo coste, fáciles y rápidos de reemplazar y los cuales no son críticos para la buena ejecución de la instalación.
Conclusión
La implantación del Mantenimiento Centrado en Fiabilidad o RCM, utiliza la base de la Ingeniería RAMS para el desarrollo de los planes de mantenimiento de la instalación o sistema bajo análisis. La experiencia en diferentes industrias conocidas por la criticidad de su mantenimiento como la aeroespacial, ferroviaria, nuclear o oil&gas, han reportado, gracias a la implantación de la metodología RCM, reducciones de costes en las actividades de mantenimiento, mejorando en la mayoría de veces, la fiabilidad de sus operaciones y por tanto la disponibilidad global del sistema.
Si mejoramos la fiabilidad de los sistemas y el mantenimiento que afecta a disponibiliad queda muy reducido la disponibilidad se ve claramente mejorada. En mayor y en menor escala la metodología RCM puede aplicarse a cualquier instalación o activo productivo con el mismo objetivo reportado por dichas empresas: reducir costes y mejorar los indicadores productivos del activo.
En Leedeo Engineering tenemos experiencia en
la implantación de esta metodología gracias al fuerte bagaje en ingeniería RAMS
que avala nuestro conocimiento. No dude en contactar con nosotros si requiere
de más información al respecto.
¿Te interesan nuestros artículos sobre Ingeniería RAMS y Tecnología?
Suscríbete en nuestra newsletter y te mantendremos informado de la publicación de nuevos artículos.