What is a Failure Mode Effects and Criticality Analysis (FMECA)?
The FMECA (Failure Mode, Effects, and Criticality Analysis): Failure Mode, Effect and Criticality Analysis (FMEA)) is a methodology to identify and analyse all the potential failure modes of the different parts of a system, the effects these failures may have on the system, how to avoid the failures and/or mitigate their effects on the system.
In other words and in simpler terms, the MECA is a technique for identifying, prioritising, and eliminating possible system failures (at design or process level). The FMECA basically differs from the FMECA Design and FMECA Process in the following: the first one refers to the product or system, the second one focuses on the problems derived from manufacture, maintenance, or operation of the equipment.
Initially the FMECA was called FMEA or AMFE. The C is a new parameter that is increasingly used, which indicates the criticality or seriousness of the various effects of the failures, being able to prioritize their importance.
Why an FMECA is used?
- Having an objective criteria for selecting design alternatives during the initial phases of a product or system development.
- Have a method for considering all possible failure modes, as well as their effects.
- Listing possible failures and identify the importance of their effects.
- Developing criteria to execute a robust and effective testing plan for problem detection.
- Accumulating knowledge for future developments and design changes.
- Providing a basis for maintenance planning .
- Providing a basis for reliability analysis RAMS.
How do we carry out a FMECA? Here are the 4 essential steps of a process Failure mode effects and criticality analysis (FMECA)
Step 1: Preparation of FMECA
Initially, the system to be analysed must be correctly defined with a clear understanding of the limits of the system, i.e. which parts must be included, and which are excluded from the analysis FMECA. We must consider that the interfaces of the limit of the equipment to be analysed must also be included in the analysis. It is also important to be clear about the operational and environmental conditions to be considered. Temperature or mechanical stress, for example, play a major role in equipment failure modes.
On the other hand, it is important to have all the necessary information about the system to be analysed, including diagrams, block diagrams, list of components, interface information, functional descriptions, etc. FMECA is carried out with an understanding of what the system does because it must be seen how failures affect the proper functioning of the system. Therefore, understanding what functioning means is necessary. Finally, if available, we always recommend using the return of experience (REX) on similar processes and/or similar products from the past. We also recommend consulting the suppliers of the components that we are going to analyse our intention to carry out a FMECA , aiming they send us all the information about their components.
Step 2: Analysis of system structure
Carrying out FMECA may be seen as something impossible to manage due to its complexity and laboriousness. Thus, the system must be divided into manageable units or components, generally in a way that makes sense from the point of view of the system architecture developed for creating the product. From here, we must make small FMECAs from each block obtaining totalised failure modes from each block to see how these ones affect some components, in relation with others. Obviously, whenever possible, the analysis should be simplified. In most cases, this implies analysing the "higher the better", the failure modes of the components. The more we go down to atomic analysis -to minimum component-, the more difficult the system tends to be. Although sometimes, especially the first few times when no components are reused, , it is absolutely necessary. As it is identified, using reused blocks of an architecture and where FMECA is already done, it will represent a particularly important advantage in time and cost.
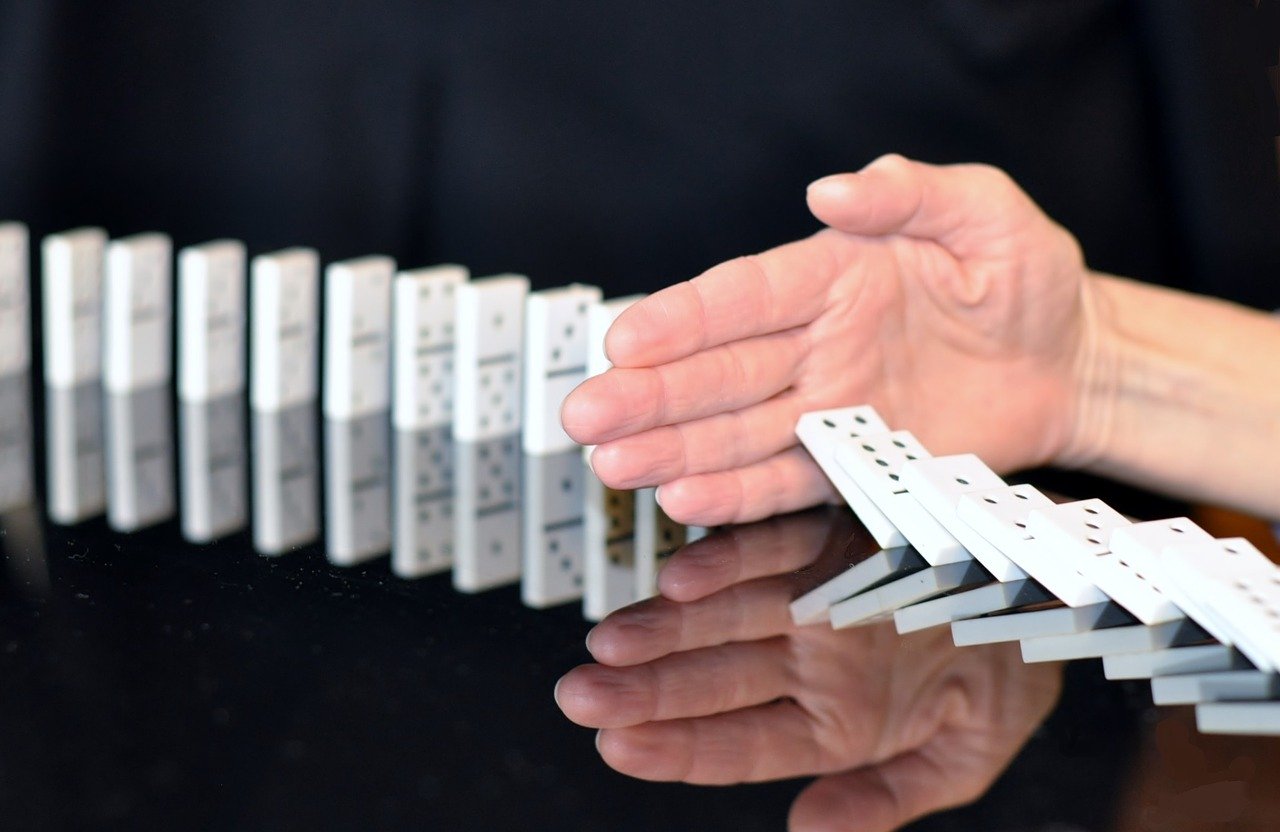
Step 3: Failure analysis and preparation of Failure Modes, Effects and Criticality Analysis (FMECA) tables
For the first FMECAs that will be carried out, the company must decide which template to use. The template is usually summarized in a few columns in a spreadsheet or using some specific tool for the development of FMECA. Leedeo Engineering recommends to its clients the following template, as a basis for creating their own as they evolve and gain experience in this type of activity.
For each element of the system the analysis must consider all the functionalities of the elements in all their operating modes and analyse whether any failure of the element may result in an unacceptable effect of the system.
In RAMS systems where safety is a design factor, we usually recommend extending in the "Effect Produced in the System", a new row with the following columns to check effect on safety, effect on reliability.
Step 4: Review of implemented FMECA and corrective actions
Once the complete analysis FMECA has been carried out, it is customary to carry out a pooling exercise, in which it is recommended that all the components of the project team participate: the project manager, the design engineer and the process engineer, the RAMS engineer, the engineer being responsible for maintenance, etc.
The objective of the work team is to study the worksheets of FMECA to decide whether the system is acceptable as it is, to identify feasible improvements to the system and those that will finally be implemented in the order of priority. Without being strict, we recommend using this "check-list" normally to look for solutions to problems detected : design changes, changes in procedures or in the way the equipment should be used, change of components -such as different failure modes-, use of systems or devices to warn of any event generating a failure, plus mitigating the effects with new additions to design.
Conclusion
A FMECA, FMEA, AMFE or AMFEC are typical and necessary activities of a process of analysis RAMS. To have a system or product under control from the point of risk, it is essential to know how it fails, to be able to predict and mitigate unwanted events in advance. We have extensive experience in developing these RAMS activities.
At Leedeo Engineering, we are specialists in the development of RAMS Railway projects, applying CENELEC standards EN 50126, EN 50129, EN 50128, EU Implementation Regulation 402/2013 with the application of the Common Safety Methods CSM-RA, supporting any level required to RAM and Safety tasks, in the development and certification of safety products and applications.
Are you interested in our articles about RAMS engineering and Technology?
Sign up for our newsletter and we will keep you informed of the publication of new articles.